IoT Vibration Monitoring for Predictive Maintenance
Introduction:
IoT (Internet of Things) vibration monitoring is revolutionizing how industries maintain their machines and equipment. Through sensors embedded in machinery, IoT vibration monitoring captures real-time vibration data and transmits it to connected systems for analysis. This technology serves as a predictive maintenance tool, detecting anomalies and identifying issues before they become costly problems.
For industries that rely on complex and expensive machinery—like manufacturing, oil and gas, and transportation—this combination of IoT and predictive maintenance offers a strategic advantage. It means fewer unplanned downtimes, reduced repair costs, and optimized machine performance.
Why Predictive Maintenance Matters
Predictive maintenance shifts equipment upkeep from reactive (fixing when something breaks) to proactive (anticipating and preventing issues). It works by utilizing real-time data analyzed through advanced algorithms to predict potential failures. According to a McKinsey report, predictive maintenance can reduce machine downtime by 30-50% and cut maintenance costs by up to 20-30%.
However, predictive maintenance isn’t limited to just improving the bottom line—it also enhances safety. Machines operating at suboptimal vibration levels pose risks that could lead to accidents in high-stakes environments. IoT vibration monitoring provides early warnings, significantly improving workplace safety.
How IoT Vibration Monitoring Works
1. Sensors Capture Vibration Data
IoT-enabled sensors, such as accelerometers or gyroscopes, are installed on machines to measure their vibration levels. These small yet powerful devices collect detailed data like frequency, amplitude, and overall vibration trends.
2. Data Transmission
The captured data is transmitted in real-time, often via wireless networks, to central cloud-based platforms or on-premises databases. IoT sensors ensure that even the smallest deviations in vibration patterns are flagged for analysis.
3. Data Analysis via Predictive Algorithms
Here’s where the magic happens. Advanced analytics tools process the vibration data to identify irregularities or anomalies. Machine learning algorithms recognize patterns to predict when a machine might fail or require servicing.
4. Alerts and Actions
When abnormal vibration levels or patterns signal potential problems, alerts are generated and sent to relevant system administrators or machine operators. This allows decision-makers to schedule maintenance checks before the issue escalates.
Key Benefits of IoT Vibration Monitoring
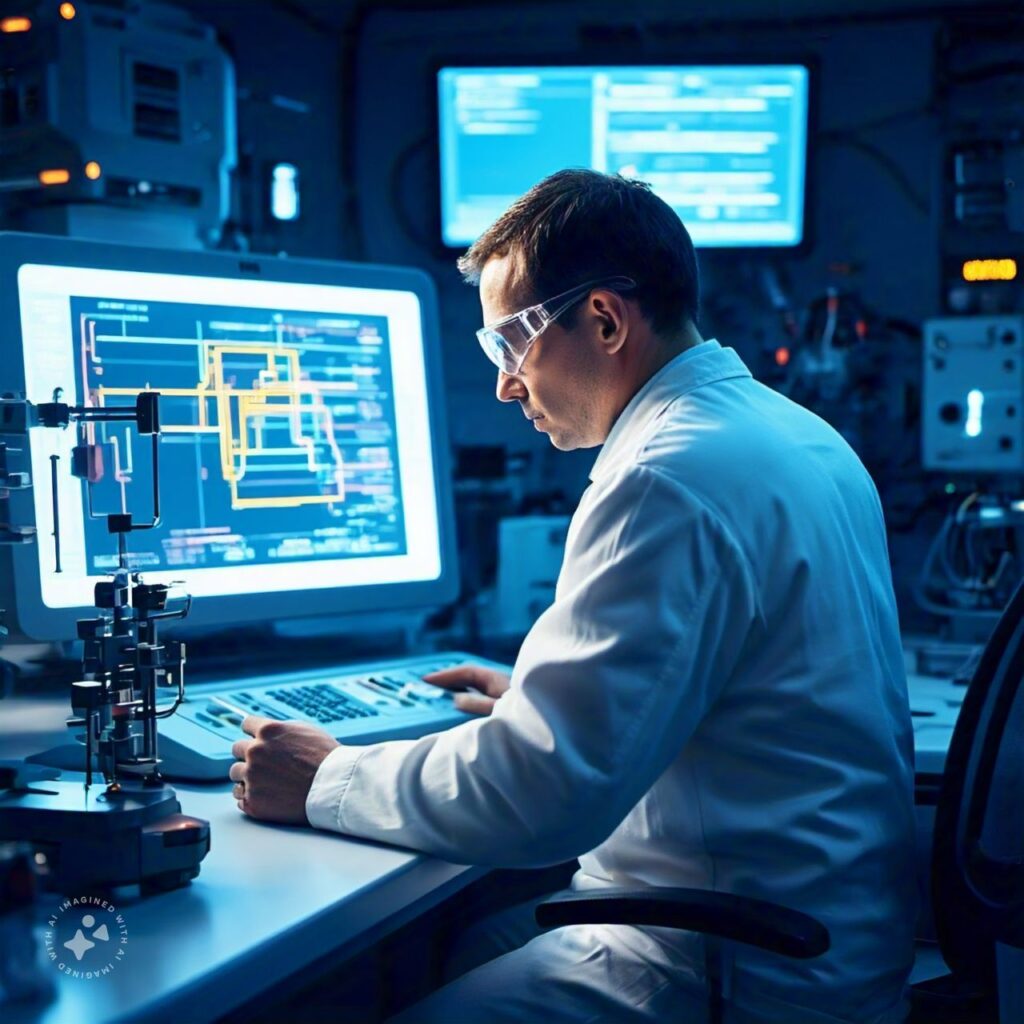
1. Reduced Downtime
With predictive insights, organizations can identify issues before they result in costly breakdowns. This means fewer emergency repairs and minimal disruptions to daily operations.
2. Cost Savings
Instead of relying on periodic maintenance or emergency fixes, predictive maintenance ensures you only pay for servicing when necessary. Over time, this approach saves money on repairs, replacement parts, and labor costs.
3. Prolonged Equipment Lifespan
Efficient monitoring through IoT minimizes unnecessary wear and tear on machines. By addressing potential issues early, organizations can extend the lifespan of critical equipment.
4. Enhanced Safety
Continuous monitoring of machine vibrations means hazards are detected promptly. This translates to safer working conditions and reduces the likelihood of operational accidents.
5. Better Decision-Making with Real-Time Data
The real-time insights provided by IoT vibration monitoring empower managers and workers to make well-informed decisions about machine maintenance and resource allocation.
Key Applications of IoT Vibration Monitoring
1. Manufacturing
Factories rely on heavy machinery, such as conveyor belts, motors, and pumps. Any downtime on these machines can slow down production or halt operations entirely. IoT vibration monitoring ensures these critical assets work effectively without interruptions.
Example
A global automobile manufacturer implemented IoT vibration monitoring on their robotic assembly arms. By identifying early warning signs of misalignment or damaged bearings, they reduced downtime by 45% and saved millions annually.
2. Oil and Gas
The oil and gas sector deals with high-risk equipment like compressors and turbines. Equipment failure during extraction or processing can lead to catastrophic environmental or financial consequences. Vibration monitoring helps maintain smooth operations in this volatile industry.
Example
An offshore drilling company installed IoT vibration sensors on its equipment. Within a year, they minimized unplanned shutdowns and saved up to $500,000 in avoided repair costs.
3. Aviation
Airline engines operate under significant stress. Even the slightest failure can have serious safety implications. Vibration monitoring ensures planes are in top condition before each flight, enhancing passenger safety and optimizing maintenance schedules.
4. Energy
The energy sector, including wind turbines and hydropower plants, benefits significantly from vibration monitoring to keep turbines in optimal working condition.
5. Transportation
Fleet managers use IoT vibration monitoring to track the health of trucks, ships, and trains. This prevents vehicle failures during transit and ensures timely deliveries.
Challenges and Considerations
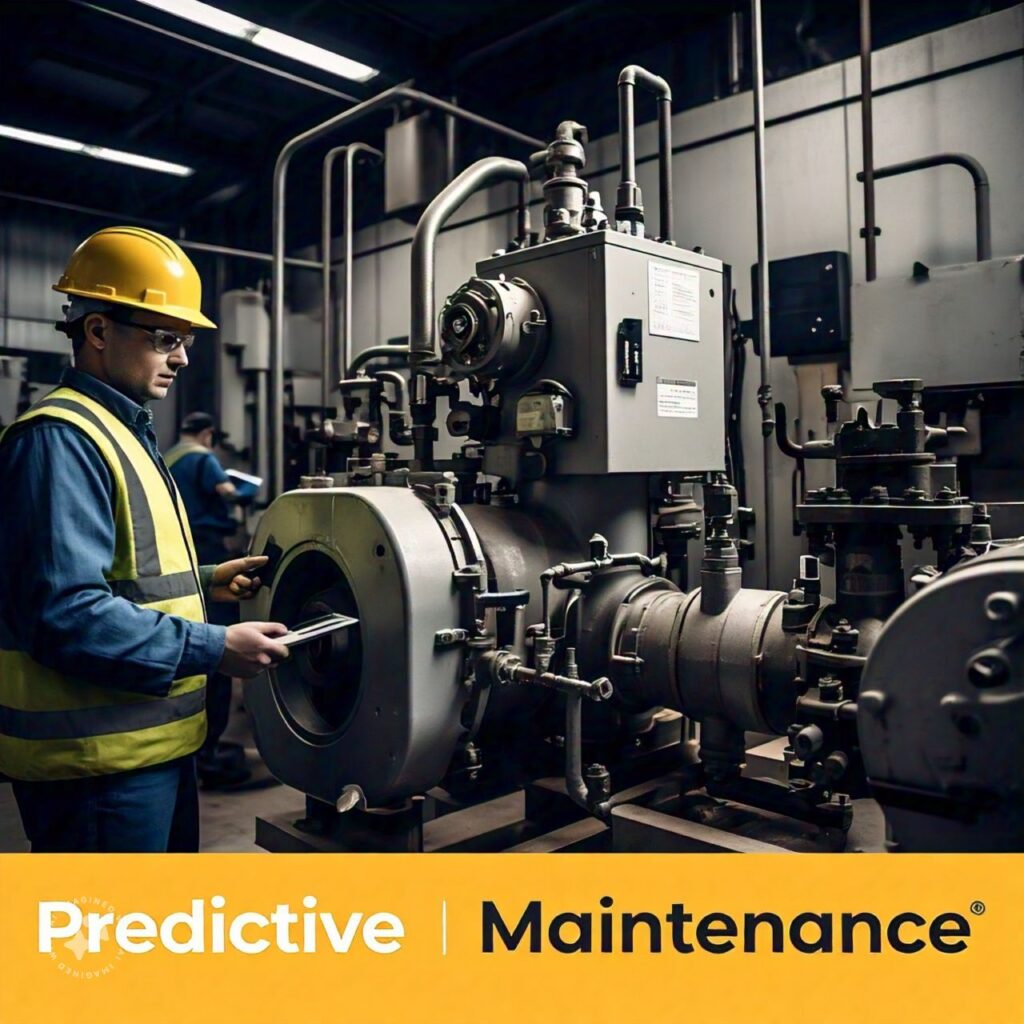
While IoT vibration monitoring offers numerous benefits, there are also challenges to address during its implementation.
1. Cost of Implementation
While IoT sensors and platforms are more affordable than they were a few years ago, the initial setup costs can still be a hurdle for small and medium-sized enterprises (SMEs).
Solution: Start small by monitoring critical assets first before expanding to others.
2. Data Overload
Continuous real-time data collection can lead to data overload if there’s no adequate processing system in place.
Solution: Use platforms powered by AI and machine learning to filter and analyze only the most crucial data.
3. Connectivity Constraints
Poor connectivity in remote locations can hinder the transmission of real-time vibration data.
Solution: Consider hybrid approaches where data is temporarily kept on sensors and transmitted when connectivity improves.
4. Employee Training
For many businesses, IoT represents new territory. Employees may need training to interpret sensor data and act on alerts effectively.
Solution: Make training simple and ongoing. Build confidence through hands-on experience with the systems.
5 Easy Steps to Implement IoT Vibration Monitoring
- Prioritize Critical Equipment: Begin by identifying the machines whose failures would cause maximum disruption to your operations.
- Choose the Right Sensors: Select sensors that suit the vibration frequencies and characteristics of your equipment.
- Set Baseline Data: Record and analyze initial vibration levels to establish what “normal” looks like for each machine.
- Monitor and Analyze Trends: Use IoT analytics tools to map pattern deviations and predict potential failures.
- Act on Insights: Use the alerts to schedule preventive maintenance before issues escalate.
The Future of IoT Vibration Monitoring
IoT technology, along with AI, is continuously evolving. The future will likely bring even more sophisticated vibration monitoring capabilities. Predictive analytics will grow smarter, while integration with other technologies like augmented reality (AR) tools may allow maintenance teams to visualize equipment health with real-time AR overlays.
Furthermore, as 5G networks become more widespread, connectivity issues in remote areas will fade away, enabling seamless, low-latency data transmission. Businesses that adopt IoT vibration monitoring now will find themselves ahead of the curve, gaining a lasting competitive edge in their industries.
Take Proactive Steps Towards Efficiency
IoT vibration monitoring is transforming how businesses handle maintenance by taking the guesswork out of equipment upkeep. From cost savings to enhanced safety, the benefits are clear.
If your organization hasn’t yet adopted IoT vibration monitoring, now is the time to explore its potential. Moving towards predictive maintenance not only enhances operational efficiency but also keeps you competitive in an increasingly tech-driven world.
Conclusion
IoT vibration monitoring is transforming the way industries approach maintenance and equipment care. By enabling real-time data collection, early fault detection, and seamless integration with existing systems, these solutions help businesses reduce downtime, optimize resources, and enhance operational efficiency. Though initial setup costs may vary, the long-term benefits significantly outweigh the investment, making it a valuable tool for both large enterprises and small businesses. Adopting IoT vibration monitoring is not just a technological upgrade—it’s a proactive step towards a smarter, safer, and more sustainable future.
FAQs
1. What types of machines benefit most from IoT vibration monitoring?
Manufacturers, industrial facilities, and maintenance crews benefit most from IoT vibration monitoring to detect equipment issues early.
2. How reliable are IoT vibration sensors?
IoT vibration sensors are generally reliable for monitoring equipment performance and detecting potential issues. They provide real-time data that can help identify maintenance needs and prevent downtime.
3. Can IoT vibration monitoring integrate with existing systems?
Yes, IoT vibration monitoring can integrate with existing systems.
4. Do IoT vibration monitoring systems require ongoing maintenance?
Ongoing maintenance is typically required for IoT vibration monitoring systems to ensure reliable performance. Regular inspections, sensor calibration, and software updates are often necessary.
5. Is IoT vibration monitoring affordable for small businesses?
IoT vibration monitoring can be affordable for small businesses, with options starting at around $500 per sensor.