IoT’s Role in Smart Factory Automation
The Internet of Things (IoT) is transforming industries across the globe, and manufacturing is no exception. By enabling seamless communication between machines, devices, and systems, IoT introduces a new level of efficiency in factory automation, allowing “smart factories” to reach their full potential.
But what exactly does IoT bring to the table for manufacturing, and how does it drive factory automation? This article explores IoT’s applications, benefits, and impacts on smart factory automation, providing practical insights for businesses ready to innovate and stay ahead in a competitive global market.
What is IoT in Smart Factory Automation?
IoT refers to the network of interconnected devices that communicate and exchange data in real time. When applied to factory automation, IoT includes technologies that link machinery, sensors, edge devices, cloud platforms, and software. These systems work together to collect, analyze, and act upon data, creating a fully connected and intelligent manufacturing ecosystem.
A “smart factory” uses IoT tools to streamline processes, monitor performance, and reduce manual intervention. From predictive maintenance to real-time inventory tracking, IoT’s role in these automated environments cannot be overstated.
The Core Components
- Sensors and Actuators
Sensors collect key operational data like temperature, pressure, and performance levels, while actuators make physical adjustments based on these readings. Together, they form the backbone of IoT systems in smart factories.
- Connectivity
Connected networks use protocols like Wi-Fi, Bluetooth, or 5G to allow machines to “talk” to each other and to centralized command centers. This seamless communication fosters collaboration between different parts of a factory.
- Cloud Platforms
Cloud storage allows the large volumes of data gathered from devices to be processed, analyzed, and visualized. This is essential for transforming raw data into actionable insights.
- Edge Computing
Edge computing performs data processing closer to devices, minimizing latency and improving efficiency. It is particularly useful in manufacturing environments where real-time decision-making is critical.
Why IoT is Perfectly Suited for Factory Automation
IoT aligns seamlessly with factory automation due to its ability to perform tasks automatically and continuously optimize processes. By eliminating silos and improving transparency, IoT enables manufacturers to create smarter workflows and improve overall productivity.
Key Benefits of IoT in Smart Factory Automation
1. Enhanced Productivity and Efficiency
IoT drastically reduces downtime by enabling machines to self-diagnose issues and machines can adjust performance to avoid unnecessary wear or breakdowns.
For example, General Electric’s Brilliant Factory initiative used IoT to optimize production times by up to 20%.
2. Predictive Maintenance
Rather than waiting for machines to fail, IoT devices monitor equipment health in real time and flag issues before they become critical. Predictive maintenance extends the life of machinery, reduces repair costs, and ensures uninterrupted operations.
3. Data-Driven Decision Making
IoT generates vast amounts of data, which—when analyzed—provides actionable insights. Manufacturers can track performance, pinpoint inefficiencies, and make informed decisions to prioritize improvements.
4. Real-Time Inventory Management
IoT-powered inventory systems monitor stock levels in real time, reducing overproduction and ensuring that raw materials and components are available when needed. For instance, sensors can track the movement of goods within a supply chain, improving accuracy and reducing waste.
5. Cost Savings
Although IoT implementation may require initial investments, the long-term cost savings through improved resource utilization, reduced downtime, and lower energy use are significant. Global manufacturers often report ROI within a few years of adopting IoT solutions.
6. Improved Safety and Compliance
IoT can track environmental conditions in factories, such as air quality and noise levels, ensuring worker safety and adherence to regulatory standards. Wearable IoT devices for employees further enhance workplace safety by issuing alerts during hazardous situations.
Real-World Applications of IoT in Smart Factories
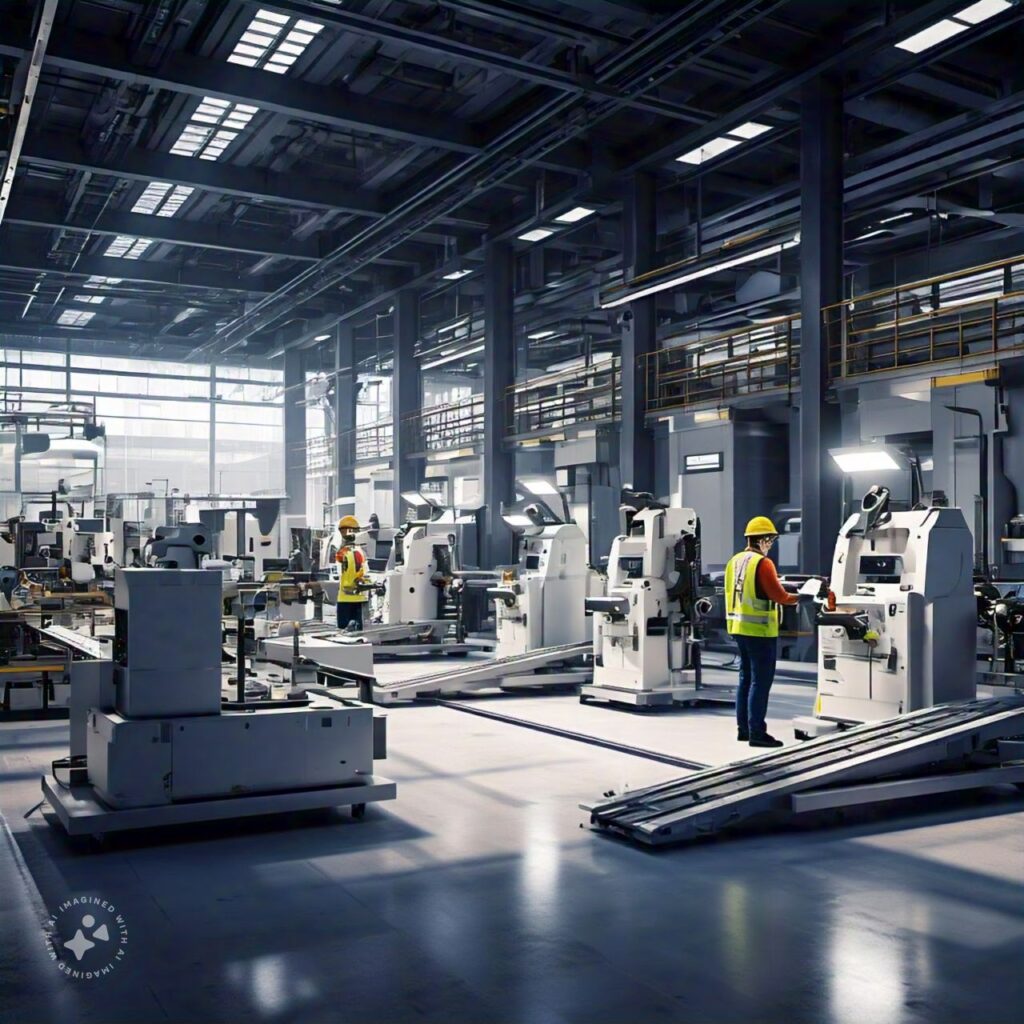
Example 1. Bosch’s Connected Industry
Bosch has pioneered the use of IoT in manufacturing, incorporating connected sensors in its factories to reduce downtime and enhance production efficiency. Its smart factory solution increased productivity by 25% across its European plants.
Example 2. Tesla’s Gigafactories
Tesla’s Giga factories leverage IoT to optimize automation in battery production. Connected devices and data-driven insights from IoT systems enable precise monitoring of processes to ensure top-tier quality and enhanced speed.
Example 3. Siemens’ Mind Sphere
Siemens developed Mind Sphere, an open IoT operating system that connects factory assets, enabling predictive maintenance, energy efficiency, and streamlined operations across sectors.
How to Successfully Integrate IoT into Your Factory
The road to creating a smart factory starts with a strategic, phased approach toward IoT integration. Here’s a step-by-step guide:
- Assess Current Infrastructure
Identify gaps in your current systems that IoT can address, whether it’s inefficiencies in machine maintenance or a lack of real-time tracking.
- Set Definable Goals
Outline what you want IoT to achieve, like reducing downtime by 15% or improving energy usage by 10%.
- Start Small
Implement IoT in one area of your factory as a pilot project. Learn from the implementation process and measure results before scaling up.
- Invest in the Right Technologies
Choose IoT platforms and tools that suit your business needs, from edge computing to cloud analytics.
- Train Employees
Introduce your team to IoT operations, ensuring they understand the tools and processes.
- Monitor and Optimize
Continuously track the performance of your IoT-enabled systems and make data-driven adjustments to improve outcomes over time.
Common Challenges
While IoT delivers numerous benefits, manufacturers need to be aware of potential obstacles:
- High Initial Costs
IoT devices, cloud storage, and data processing can present high upfront expenses. However, ROI typically justifies these costs.
- Data Security Risks
Factories handling sensitive information must secure IoT systems against potential cyberattacks.
- Integration Complexity
Connecting legacy systems to IoT platforms often requires significant effort and expertise.
Clear planning and the right partner ecosystem can mitigate these challenges and ensure smooth IoT adoption.
Transform Your Business with IoT
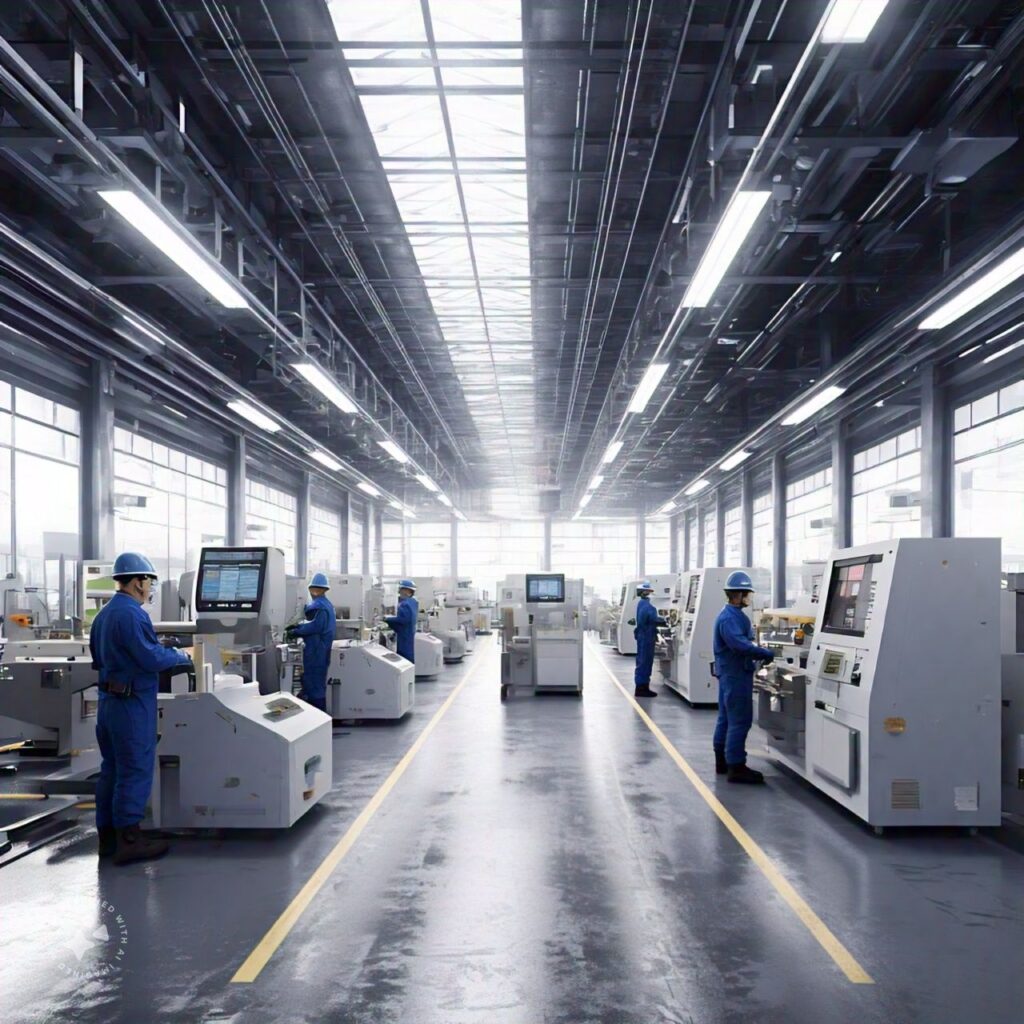
IoT is no longer a futuristic concept; it is shaping factories and industries today. From predictive maintenance to real-time monitoring, IoT empowers manufacturers to be more agile, productive, and cost-effective.
Whether you’re a small business or a large enterprise, adopting IoT in your factory can revolutionize your operations. Start by assessing your factory’s needs and gradually implementing IoT technologies tailored to your goals.
IoT offers immense potential—seize the opportunity and take the next step toward smarter manufacturing today.
Conclusion
The integration of IoT into manufacturing is no longer optional—it is essential for staying competitive in today’s rapidly evolving industrial landscape. By leveraging IoT technologies, factories can unlock unprecedented levels of efficiency, productivity, and innovation. No matter the size of your operation, the benefits of IoT are within reach. Take the initiative to explore IoT solutions and implement them incrementally, paving the way for a smarter and more connected future for your business.
How does IoT differ from traditional factory automation?
IoT focuses on interconnected, data-driven systems that optimize workflows and enable real-time decision-making, while traditional factory automation often relies on predefined scripts without continuous adaptability.
What is the cost of implementing IoT in factories?
Costs vary based on size, scope, and technologies. However, businesses typically start seeing ROI within 1-3 years post-implementation.
Are IoT-based systems scalable?
Absolutely. IoT systems are designed to be modular and scalable, allowing manufacturers to expand adoption across their operations gradually.
What industries benefit the most from IoT factory automation?
Automotive, electronics, pharmaceuticals, and consumer goods industries are among the top beneficiaries of IoT in manufacturing.
Do small factories need IoT too?
Yes, even smaller operations benefit from reduced costs, improved efficiency, and enhanced safety when adopting IoT systems.